PRODUCT DEVELOPMENT: EMBRACING PRODUCT SAFETY AND COMPLIANCE
- Share
- From
- https://www.utilitydive.com/topic/storage/
- publisher
- Anna Liu
- Issue Time
- Jul 21,2023
Summary
Solar panel power generation is a process of directly converting light energy into electrical energy by utilizing the photovoltaic effect generated by the semiconductor interface.
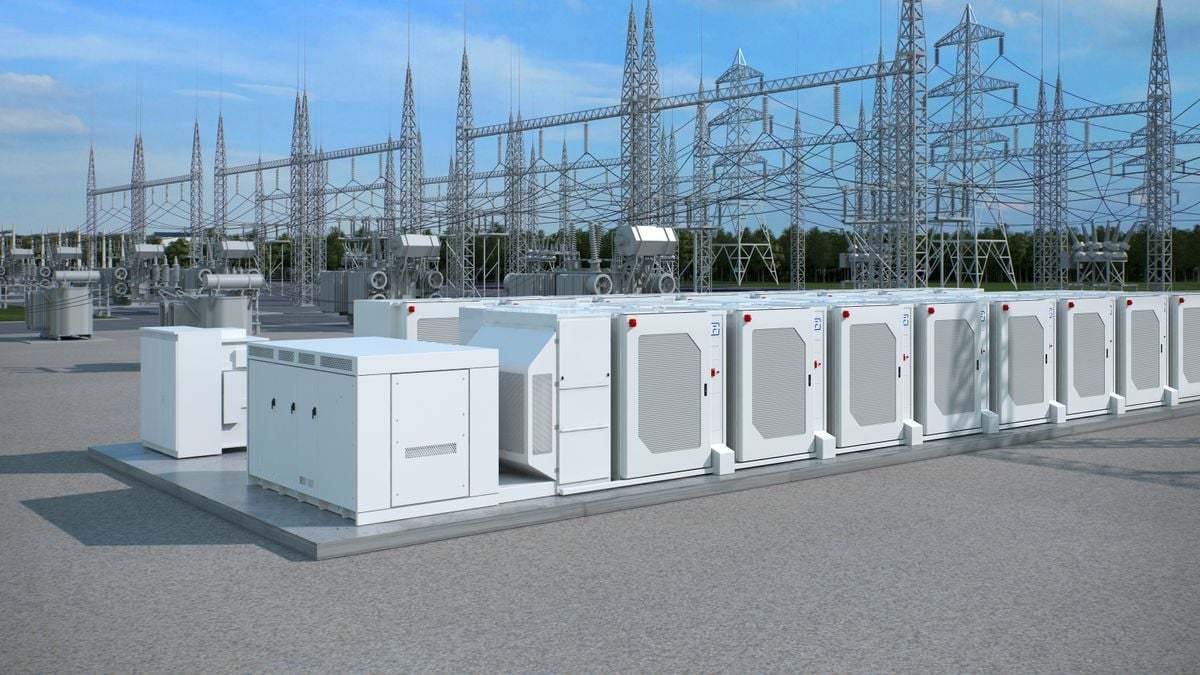
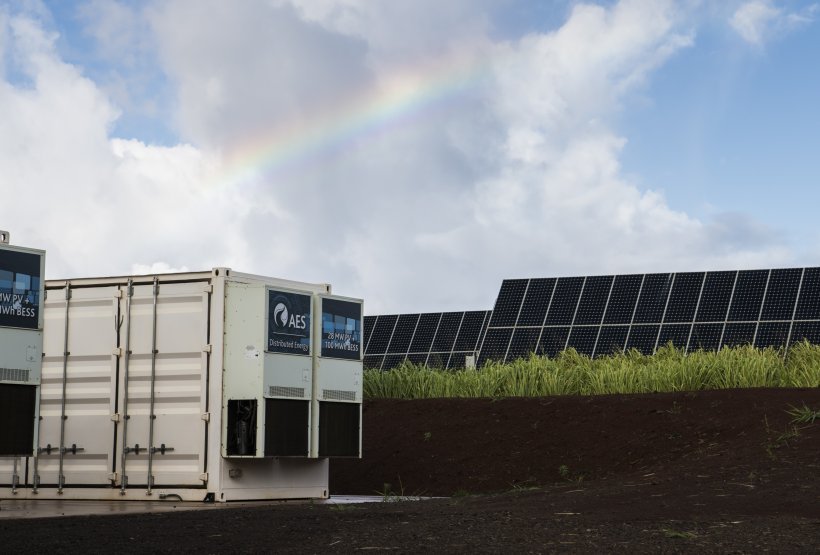
PRODUCT DEVELOPMENT: EMBRACING PRODUCT SAFETY AND COMPLIANCE
PRODUCT DEVELOPMENT: EMBRACING PRODUCT SAFETY AND COMPLIANCE
Recent safety incidents on storage plants have raised concerns about the fire safety of battery storage systems. Such events are extremely rare compared to the cumulated global deployments of energy storage systems, which have reached more than 27 GWh by end of 2020 (Wood Mackenzie 2021). However, for achieving project success and ensuring the safe operation of battery storage systems, it is indispensable to address safety in a comprehensive and transparent manner.
Energy storage solutions need to be smart, cost-efficient and tailored to the dedicated application scenario. But here is what makes a real difference to the solution: a highly experienced engineering team, highest safety standards, transparency and in-depth technological expertise for designing the key features on product and plant level to maximize personnel and product safety. A comprehensive understanding of the entire storage system is the ideal guideline to safe product development within the energy storage industry.
Battery technology & highest safety standards
Battery technology is key for a high-performing battery storage system. Lithium-ion batteries are certainly the technology to go for in the next years, thanks to their high energy density and performance. Comparing the two commonly used Li-ion technologies, there is consensus in the industry that the demand for lithium iron phosphate (LFP) batteries will rise rapidly in the near future, with an estimated demand of more than 17 GWh for the energy storage industry only in 2022 (IHS Markit 2021). At the latest in 2024, LFP is expected to become the main technology used for energy storage. The rising demand is mainly coming from lower costs and a lower supply chain risk as well as higher durability and performance. Along with that, their safety advantage over nickel manganese cobalt (NMC) is one of the main drivers. Higher temperature resistance enables a reduced risk of thermal runaway through overcharging, short circuits or approaching the end of life.
What is also one of the fundamental indicators for a safe solution is regulatory compliance. Storage providers look more and more into the activities of the leading certification authorities to regulate the product landscape. While one might see those ever-growing requirements for compliance as a limitation for product development, Trina Storage embraces international safety standards and guides its product development along with them. Besides, federal and national regulations play also a crucial role on the project execution side. Hence, looking into the local regulations, building up an in-depth understanding and closely cooperating with all stakeholders of an energy storage project are prerequisites for engineering safe storage solutions.
For sure the most noted standard lately is UL9540A, which unlike most standards is not a certification per se that can be passed or failed but it is a Test Method for Evaluating Thermal Runaway Fire Propagation in Battery Energy Storage Systems. As such the results of the test are often referred to during certification processes for other standards, for instance, IEC’s Safety requirements for grid-integrated EES systems and electrochemical-based systems (IEC 62933) or the Standard for the Installation of Stationary Energy Storage Systems from the US American National Fire Protection Association NFPA 855. UL has also launched an energy storage safety test database where storage system operators can review the battery manufacturer’s results of their UL9540A thermal runaway propagation tests.
Fire prevention and suppression for maximized safety
Although compliance with the latest standards is an excellent guideline for developing a suitable portfolio for the market, Trina Storage wants to go further through additional fire prevention and suppression measures. The golden rule for on-site safety induction is to keep personnel safe and sound. For the sake of it, all equipment can be maintained without entering the enclosure. If there is a need for maintenance in the batteries, control boxes or thermal management system, the equipment can be accessed from outside, while a door sensor ensures that the system is automatically stopped.
In addition to those common functionalities, the industry recently has come up with a wide range of equipment to pimp an energy storage system for increased safety. The fire suppression system (FSS) ultimately serves two purposes, one is to avoid propagation of secondary fires to the batteries and the other to prevent thermal runaway within the battery system. For the first purpose, smoke and heat sensors are common sense by now, while manufacturers offer either Novec or Aerosol-based solutions as an extinguishing agent. An emergency stop function for shutdown is also part of a basic configuration, either automatically triggered by safety equipment or real-time monitoring of the EMS or manually by operators or first responders. Preinstalled sprinkler systems are activated upon smoke or heat signals but have the disadvantage that an outside water connection is needed which can be an obstacle to project requirements. An active ventilation system on the other hand is intended to minimize the impact of off-gassing batteries. It is triggered through a gas sensor when exceeding a predefined limit and will react to that by venting the batteries. Trina Storage’s recently unveiled Elementa features this kind of system. Finally, there are also deflagration vent panels emerging in new products launched on the market, a passive prevention measure intended to act as a pressure relief point within a cabinet. However, the latter is considered optional, as the right certification makes them redundant. And overall stands, of course, the suitable controls and advanced software for continuously monitoring battery performance and system safety.
After all, providing a safe and reliable energy storage system is about high-tech safety features and certification compliance but not limited to it. Having a team of engineers with the highest competencies in system engineering and project execution at your side is key for designing a secure system tailored for your needs. On behalf of all stakeholders, close cooperation between storage providers, plant developers and end-users is also beneficial for guiding the product design towards the highest safety. And finally, the local expertise of your storage provider’s team simplifies the entire planning process and increases safety for the sake of plant operation and personnel soundness.